Insights
Read our expert insights to understand industry trends shaping the future of translation, interpretation, and language solutions. Our valuable perspectives help businesses navigate communication in any language, with confidence.
Industry Insights
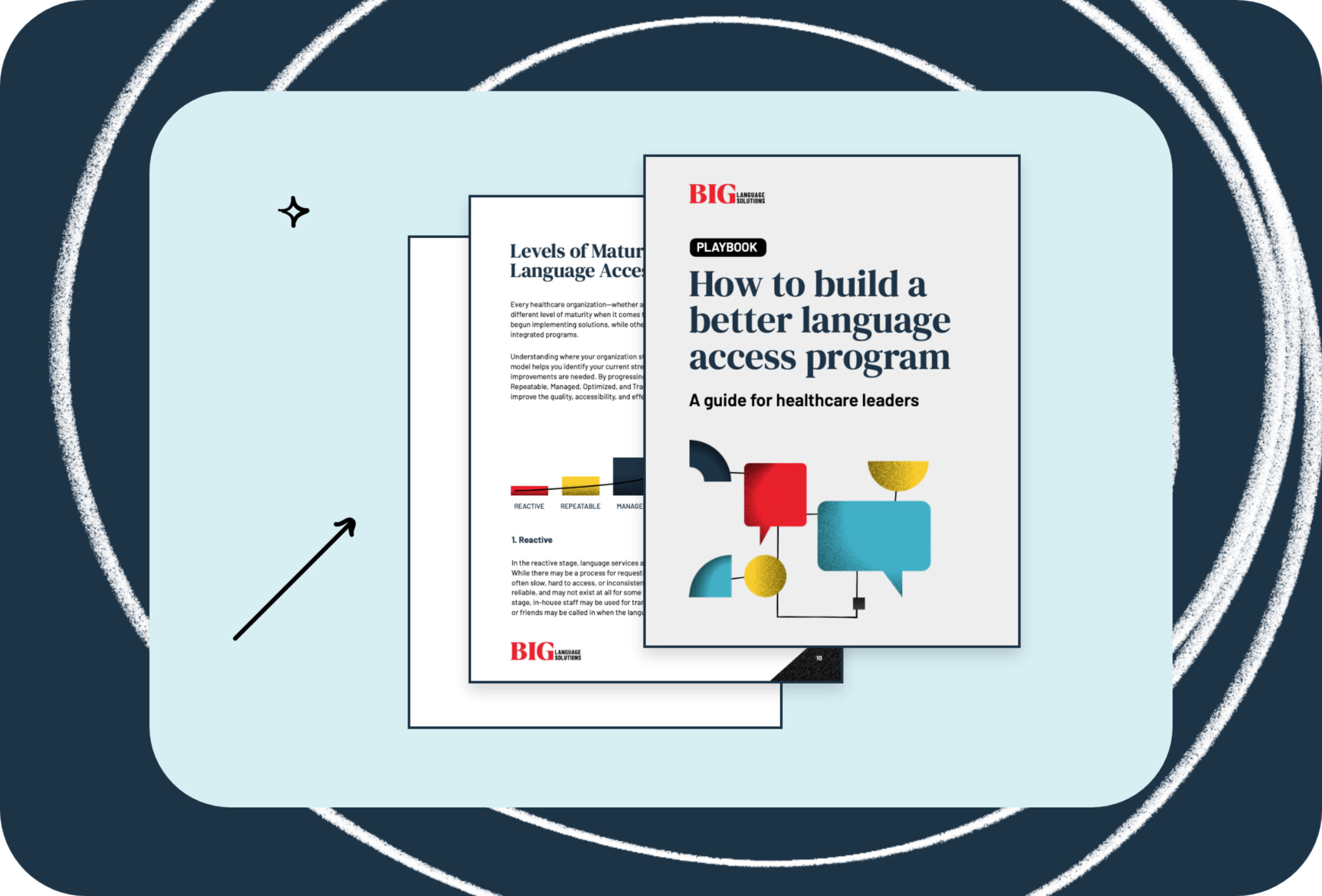
LANGUAGE ACCESS GUIDE How to Build a Better Language Access Program: A Guide for Healthcare Leaders Effective communication is essential...
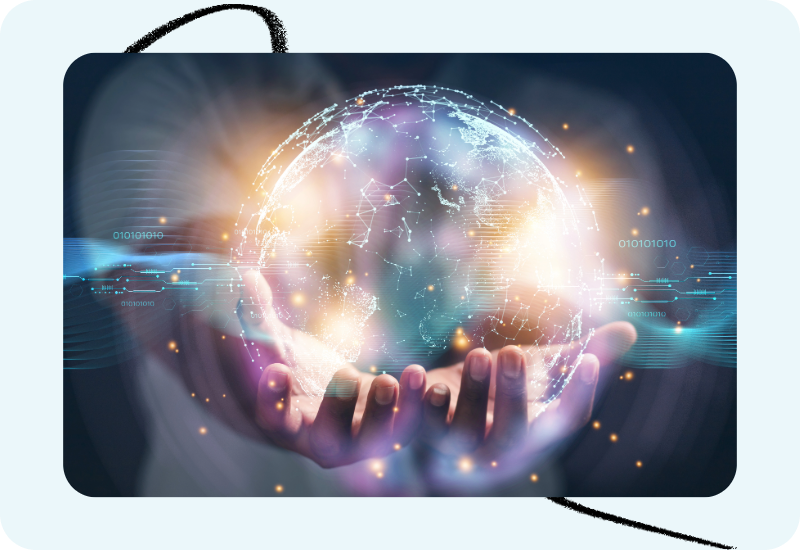
AI, Automation, and the Future of Language Services: A Conversation with Dan Nelson
Global enterprises of all types have long struggled to provide language services quickly and accurately enough to those who need
Explore by Interest
Explore by Industry
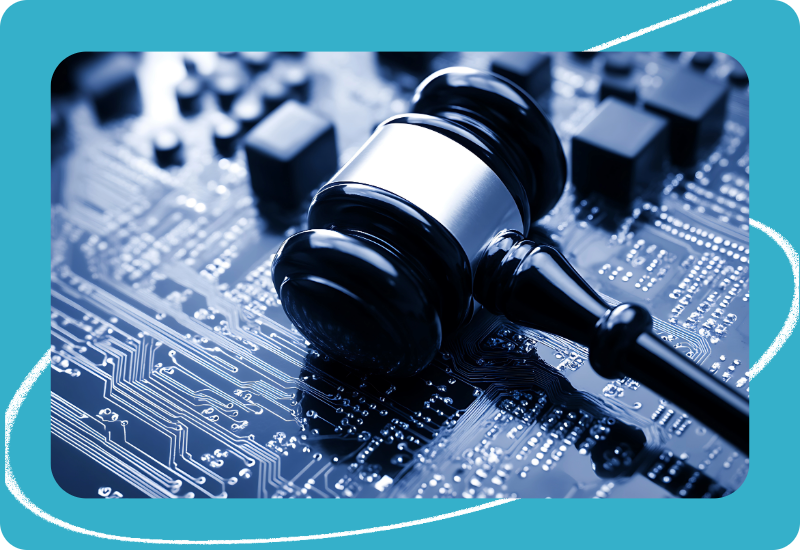
Why Patent Translations Require More Than Just Words: A Legal Insider’s Perspective
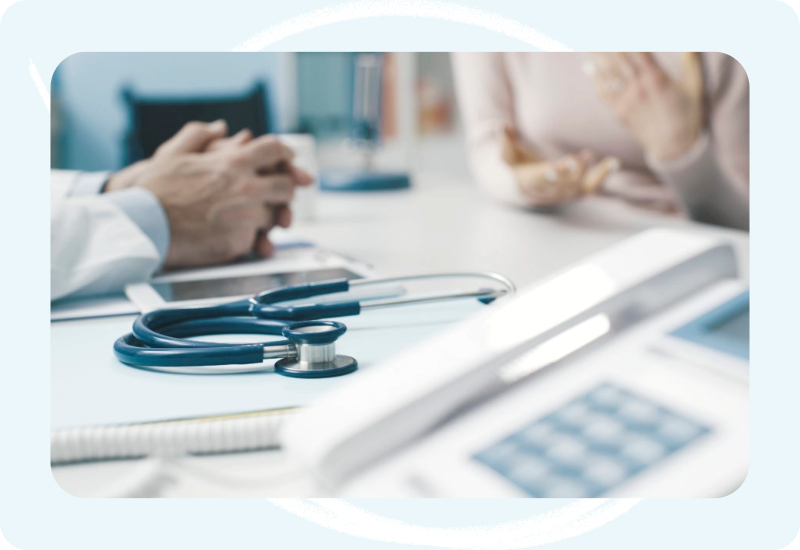
How Interpretation Improves Patient Experience in Healthcare
When patients and providers don’t speak the same language, the quality of care can suffer. Misunderstandings can delay diagnoses, confuse
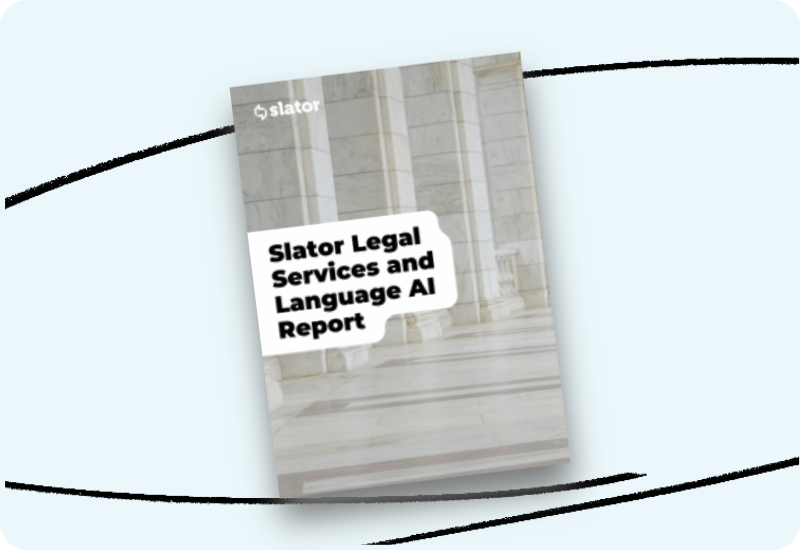
Slator 2025 Report Highlights Challenges for Language Services in Patent and Legal Industries
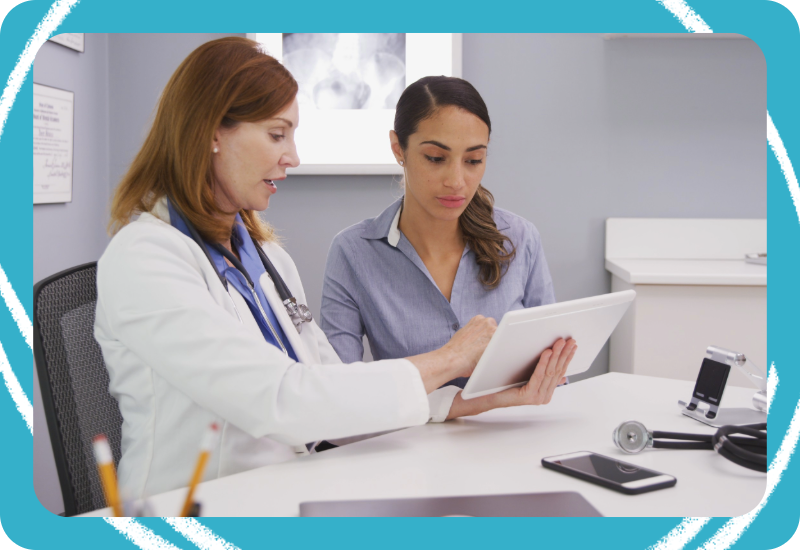
Four ways to be ready for increasing language diversity in your community health clinic
America’s population is changing—and so are the languages we speak. In fact, according to a recent study from the Brookings
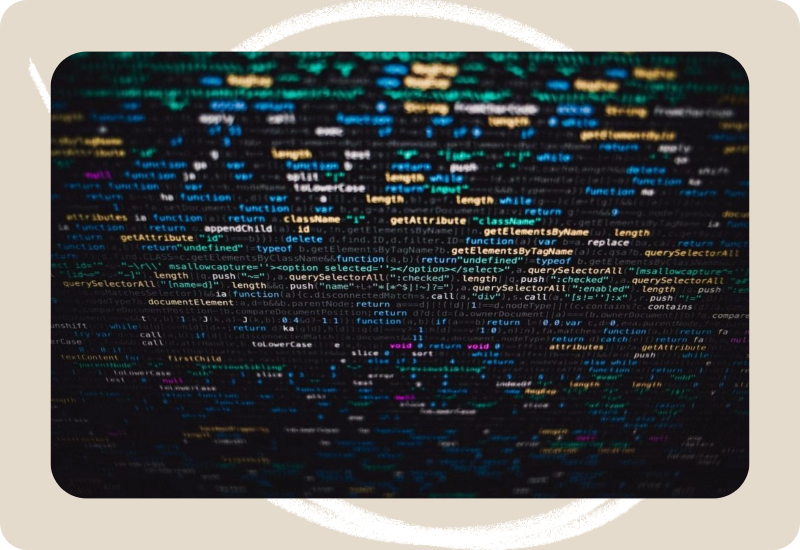
Rolling out Neural Machine Translation? Here are Four Keys to Success
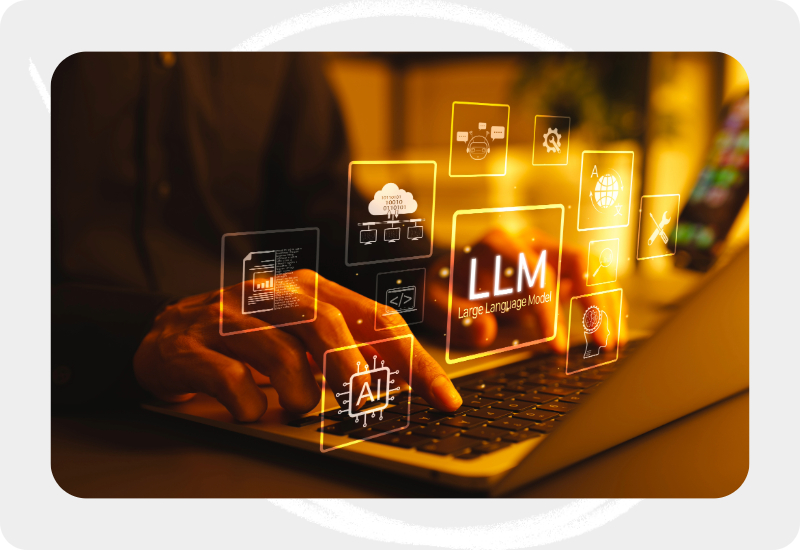
Why NMT Still Leads: Smarter, Faster, and Safer Translation in the Age of AI
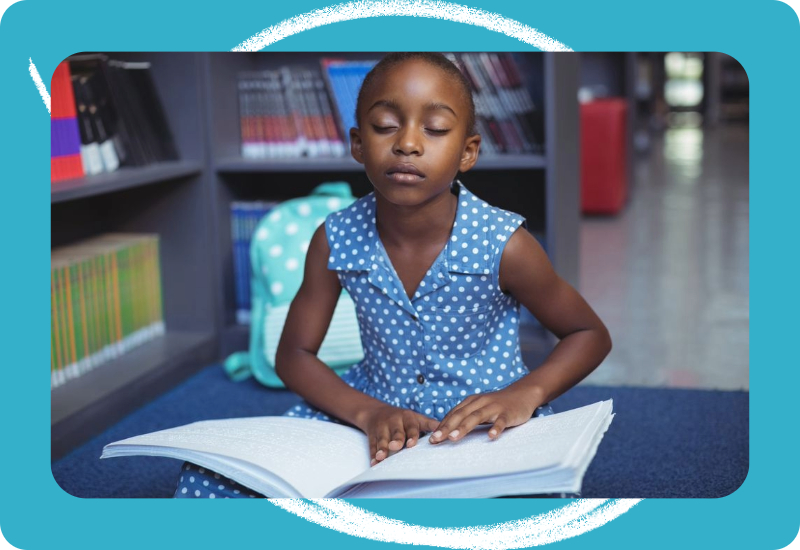
What is Section 508 Compliance?
When communicating with federal agencies, there are a variety of laws and regulations that have been established over the last
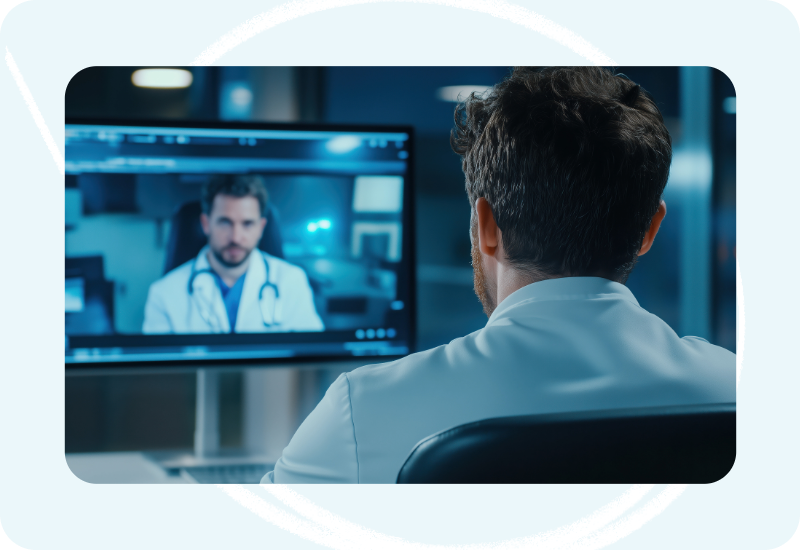
The 5 Main Types of Interpretation Services and How They Are Shifting in an AI-Powered World
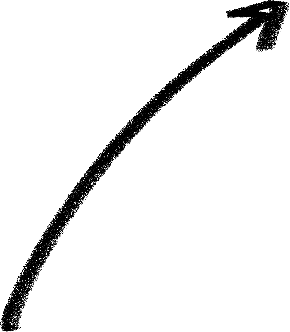
STAY IN TOUCH